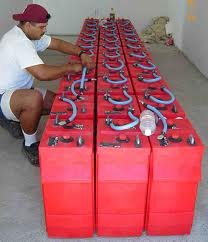
FROM YAHOO ANSWERS:
Here’s my setup: 24V battery bank (6x4V Rolls-Surrette deep cycles in series) connected to my wind and solar charge controllers as well as an inverter for my house, all in a shed about 60′ from the house. I also have a 24V panel in my garage directly connected (through a breaker) to my batteries over 100′ away at this point (voltage drop is minimal because I sized the wires right).
What I’d like to be able to do is use my vehicle as a back-up generator for when my batteries get too low (e.g. 22V) by parking it in the garage (with the door open of course) near the panel and applying a charging voltage to the panel from the vehicle. My thought is to connect a 400W inverter (I already have one in the back of my Tacoma) to a 15A, 24V battery charger and put it on a 15A breaker in my panel. Theoretically, this will raise the system voltage to the 28V charging voltage of the battery charger, which will fill the batteries. The first question is, will this work as I expect? Secondly, what if the well pump kicks on pulling 3000W? Will that trip the breaker on the charger even though the batteries, which might otherwise be at 22V, have sufficient amps to handle it? I’m not sure of the preference of where power will be pulled from. Will the battery charger be the go-to source of all household power because it’s at a higher voltage? Or will the charger merely put out as much power as it feels like and the loads won’t affect it? If the charger is going to trip its circuit every time there’s a load bigger than 15A on the system overall, then there’s no point in doing this. Otherwise, if the charger will just do its thing oblivious to anything else, then this would be a great solution for emergency battery charging for my house. I.e. I’d be jump-starting my house with my truck!
19 Responses
I have used a Alternator to charge my battery bank for the past 6 yrs.
First, you never run your battery down past 50%, doing that too many times can damage your batteries.
I use the same batteries that they use on Commercial 18 wheelers, most trucks have 4-6 1000 amp hr batteries.
Mine are rated at 1050 amp, wired for 12 volts, 10 batteries in total, with a 7000 watt full sine wave inverter.
I live in a 37′, 4 slide out 5th wheel, rated at 50 amp service, 115v.
I have 2 alternators, 160 amp output from a commercial truck. I turn the Alternator with 2 modified washing machine motors which have a dedicated inverter attached to same battery bank. I have had to replace one motor due to a bearing problem.
I am a full time RVer and the Amp draw from my camper is around 32 Amps. running 1 rooftop A/C unit and a 10 gallon electric hotwater heater, lights and the 12v converter built into camper. Alternators are never under a heavy load, battery draw is around 35-40% draw. I test batteries once every 3-4 months, I have amp meters, voltage meters and over and under volt protection.
I have been building a magnetic motor, small HP output so far. it runs my water pump that supplies water to camper.
I would like to find larger magnets to build a magnet motor equal to about 3 hp so I can run Alternators off my battery bank, free up load, that would extend life to my batteries. I have a charger controller that maintains charge to batteries. Most of the parts for my system I got from scavenger hunting, except Charge controller and wiring.
Critical features are never drain batteries past 40-50% and I oversize wires to ensure of no overheating of components.
Hope this helps.
A friend of mine in the greater Seattle area used to commute about an hour each way to work. Because of his second job, he had to use a full size pick-up, which he did in the form of a Chevrolet 1500. At the time, he lived off-grid and his solution was to put several 6v batteries (Dyno golf cart batteries) in the bed of his truck in a box, and let the alternator charge the battery bank on his commute. Then, when he got home, he simply plugged the bank in to the house using a heavy a electrical connector like they use for trailer hitch mounted winches and forklift batteries. Actually worked pretty well. I’m sure it impacted his fuel economy, but how much, I’m not sure.
A generator might be a better idea. Unless you have a pretty huge charging system on your car, you can damage your alternator and battery. This is very likely if you are charging up your system more than just after one ’emergency.’
Alrod53, assuming we went with the initial proposal of a battery charger on a 400W inverter, then that would only be 33A @12VDC. That’s only half a percent of a 6000Ah battery. It would take days to charge it. And once you start talking about circumventing the normal vehicle wiring to try to get more amperage, it defeats the original requirement of being a simple design. It also puts undue stress on the factory alternator. And again, changing the alternator is outside of the simplicity requirement.
So my conclusion is that while it may be a possible super-emergency stop-gap measure to put a 15-30A charging current on my batteries, it should be the last option only. That’s why I’ve since installed a propane generator as the first backup should my solar or wind fail. Only if the propane genny also failed and my batteries were dangerously discharged would I connect up my vehicle. And then in that case, I would ensure all loads are disconnected from the system so that the batteries could basically be on life-support until one of the primary charging sources is restored.
Hmm. How about splitting the 24 volt battery bank into two 12 volt banks and charge each bank seperately. (what are those batteries 2volt?) I use a 6000ah battery for an electric forklift that is 24 volt but split into two 12 volt banks and only use one at a time on one 6000 watt inverter. That way I always have one fully charged bank…But thats just what I think.
I’m the original poster of this question on Yahoo Answers (which was deleted for some reason). I appreciate the advice. The point was to use off-the-shelf components in a very simple setup that even my wife could operate confidently and easily. As it would be strictly an emergency configuration not to be used more than 1-2% of the time, it didn’t seem to be asking much of a vehicle. However, the points about the design of vehicle alternators and the sufficiency of the resulting charging current were taken to heart. And indeed, such a configuration is not really necessary when small gensets are relatively cheap.
So in the end, I went with a 2000 Watt Sportsman Propane Generator (rated at 1300W continuous) from homedepot.com for $299.00 and an Iota 24V 40A Smart Battery Charger from chargingchargers.com for $365.00. The total cost after shipping, wires, fuse, and propane hookup was under $750. The combo puts out nearly 1kW, which is the rated output of my wind turbine at full speed or the average output of my PV array on a partly-sunny day. In other words, plenty to charge my batteries — 7.2% of my battery bank’s rated Ah. The charger puts a roughly 75% load on the generator, making it an efficient use of fuel. It consumes about a third of a gallon of propane per hour. That means that I could run the charger for 300 hours on my 100-gallon tank.
I’ve only used it once so far (and didn’t really need to) — it brought my batteries from 23V to 26V in a matter of minutes and went to float mode within a half hour. I have it in a small well-ventilated shed along with my propane tank, which backs up to my power shed containing my batteries and stuff, and you can barely hear the generator from a few dozen feet away.
The generator is quite small and portable. I used copper pipe clamps to secure it to a table at a comfortable height to start it. It easily started below freezing. Though it does require pulling on the pull string rather than an electric ignition, it starts without too much effort. I haven’t yet had my wife try to start it though… we’ll see.
Propane was a good solution. One of the reasons I was hesitant about using an independent gas generator is because gas engines generally need to run fairly frequently or they can gum up. Diesel is often used because the engines tend to be simpler and more reliable. However, I figured I will most likely need a backup generator in the depths of winter when diesel engines are difficult to start. Gasoline and diesel also require frequent filling of the tank and are prone to spillage. Propane doesn’t have any of those problems. And since I already use propane for cooking and back-up heat, I already have a 100 gallon tank.
The car charging the house was a fun idea, but inherently flawed. I think my current solution is far superior. It provides more redundancy and prevents stressing my vehicles. It’s fairly inexpensive and simple and low-maintenance, which were the goals from the start.
A good part of a vehicles alternator power is used to recharge the vehicles own battery when the engine is running at a low rpm and would waste a lot of fuel and needless ware and tear your vehicles engine. Think about the amount of fuel you would use to operate a 150HP engine with no load! Look at using an ALTEN DC generator as a supplemental recharging device that would uses a fraction of the fuel, recharges in a fraction of the time. Or as other have said, you can build your own, if you are handy .
Best bet is to look around gov’t auctions for a niehoff altenator (stock equipment in a hummwv). It’s pretty comon to find these in 200 and 400 amp, external adjustable regulator setups, and just us an external engine to drive it.
Why don’t you just get a $500 gas powered 5000W generator and charge it with that? I suppose that would be a fraction of what you’ve spent on the batteries.
Use a heavey truck altinator for your charging they are around 130 – 150 amps output. You need to figure out the power you are useing and adjust to the usage you really need. you can hoock up a lawnmore engine to the altinator instead of running your car.
sorry elnav already said that.
why not just build a 24v generator from a 24v alternator and a small gas engine?
Just looked at the problem of charging the battery from the 12v car system, using an inverter and a charger is inneficient. Go to ‘ Adverc Battery Management’ on the web, they have a device (a DC to DC converter whivh will charge a 24v battery from a 12V battery. Ask to speak with Jenny, she will put you right.
Fjurther to my previous comment, her is a better explanation as to what happens when you try to charge a big off-grid bank from a car alternator.
Using a car alternator to charge an of grid battery bank.
This is a question that comes up time and time again. The answer depends on a lot of variables. In a few limited cases it can be done but for most installation it poses a risk to the alternator and may prove disappointing in results.
Automotive alternators were originally designed to deliver a large current for a short time to recharge a starting battery. So a 70 Amp alternator may be considered heavy duty when charging a battery on a typical 4 cylinder engine in a compact car. However if you attempt to pull 70 amps from the same alternator for a full hour or longer it will overheat and quickly die. The better models have temperature sensors that shuts down the unit while the less complex models simply burn out the rectifiers.
To deliver a charging current of 15 Amps to a battery is not sufficient except for the smallest size. The rule of thumb for charging batteries is it should be somewhere between 10% and 25% of the amp hour capacity. If you parallel two deep cycle batteries to get 200 amp hour capacity this means you need to charge with somewhere between 20 A and 50 A charging current. For best results this charging should be sustained as a constant current until the battery is 75- 80% charged. At that point a smart charger would revert to a taper charge for the remainder of the charging.
Unfortunately most automotive alternators are not equipped with a smart regulator. They are a constant voltage taper charge. Result being longer charge times and in most cases an over heated alternators.
Special alternators intended for constant current output are made. They have additional cooling provisions and more rugged components. In most cases they are also controlled by an external regulator that can be programmed to suit the installation. Most important they have temperature sensors for both battery and alternator case temperatures so if something over heats the regulator cuts back on the charge current before damage occurs.
I have seen automotive alternators rewired for these special regulators and invariably they go up in smoke because they were overloaded.
Modern auto alternators have an additional wrinkle added. If you connect on to the cable going to the battery you will find the modern versions are current limited to around 20 A and a separate wire sends most of the current to the computer controlled vehicle system. I learned this while asking my mechanic why my newer 1995 alternator had five wires instead of the older having only 3 wires. This simply makes it that much more complex to use automotive alternators.
If the vehicle is your transportation as well; my recommendation is to not mess with it.
Instead rig up a separate old style alternator and drive it with a utility engine. It will burn less fuel and if something does goes wrong it will not impair your vehicles so you can drive to town and get repair parts.
It depends on the kind of charger you have. Smart chargers with current limiting will not trip a breaker but cheap automotive types will likely overload. The original statpower ( now Xantrex) chargers can be short circuited without harm. they were designed for this duty. however your biggest problem will be your alternator. Doing what you propose will burn it out in a few days. Especially if your vehicle is built after about 1993. I did exactly what you proposed with my old 1984 diesel Ford. I parked close to the battery bank and used #4 Ga jumper cables from truck to batteries and recharged the bank every day with about an hour and a half charging. difference being that truck had a heavy duty 120 Amp alternator plus an external regulator.
Since you have a 24V system why not install a 24V alternator in addition and belt drive that to charge the battery bank directly. That is how I design all my systems now. Balmar and ample Power can supply 24V alternators as well as regulators as can several other specialty companies offering welding alternators.
The loss in all of that cabling from the panel to the battery bank will drop your charging voltage and any gain will be negligible. What is your primary charging system? Is it sized to match that battery bank?
Depending on the ah of the batteries, 15 amps might not be enough.
The batteries will act as a buffer when the loads go beyond the capacity of the charger.
Put .4ohms in series… This assumes minimum battery voltage of 22v (6 volts less than battery charger). Put .8 ohms in would let the battery voltage go down to16v, but at 22v would drop the charge rate to 6amps. Most chargers don’t need this as a battery is already able to suck a lot more than 15 amps when discharged. We charge our forklift batteries at 80 plus amps when fully discharged (I think at one time we tried 160amps)… fully discharged means lowest allowable charge. Anyway, a charger is a current source… it needs to be able to set its own max current out. Most cheaper ones choose wire size/transformer size to achieve that, some may use an assumption of lowest possible battery voltage and breaker if current is too much. I am assuming you are using this setup because you have the parts. A 24 volt alternator (some trucks use them) would be a better use of your fuel being able to charge at 60 amps or more. I don’t know the cost though… or if you have the space in your truck to mount an extra alternator.
That is a sweet setup! Can’t answer your question but maybe you can put the well on wind powered pump eh?