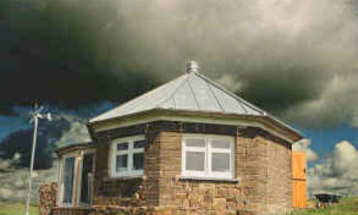
This extraordinary little house was built around 1910 as a Croquet Pavilion by Harold Fowler, an International champion. It has now been renovated as an off-grid holiday cottage, usually by the week.
A local specialist in environmentally sustainable construction, Julian Bishop, was commissioned to design an eco-cottage. The brief asked that the visual profile and footprint remain as unchanged as possible, allowing the building to maintain, but not increase its position in the landscape. The materials were environmentally sustainable: energy to come from natural sources and water to be collected from the roof. The craftsmen involved were locally based and committed environmentally. The result was that materials used have less environmental impact and are less toxic. Experience living on the coast indicated that trapping moisture is detrimental to the health of both the building and the people. Materials used allow the building to “breath” helping to prevent condensation inside.
The whole property, then known as Druidstone Villa, was bought by Lord Kensington in 1929 and sold to local surgeon, John Gillam, in 1949 as a family home. In 1972 Jane (Gillam) and Rod Bell set up a hotel in the Villa. The Roundhouse was in need of some considerable renovation. With no electricity, a coal burning stove battling with the drafts and a chemical loo in a shed, even a Spartan would have found it tricky to cope. To prevent further deterioration, as a Millennium project, it was decided to renovate it as a miniature example of sustainable living.
LIME CRETE has been used instead of concrete in the foundations, mortars and pointing. It uses less energy in the process and the transport.
LECA is vitrified expanded clay balls, rather like cat litter for tigers. It makes a dry, lightweight insulation under the floor. To stabilise it before laying limecrete slab, a natural fibre membrane and a reinforcing grid was used, otherwise it behaves like a ball pool in a children’s play area when you try to lay anything on top.
MASONITE/OSB/HERAKLITH. Masonite is a super-strong structural “I” beam made from small section soft wood and a hardboard web of solid timber. Steamed and compressed, the wood fibres bond together with their own natural glues. It does the job of a larger section of timber and avoids the cold bridging effect. OSB (orientated strand board) was used internally to the Masonite timber framing. It has lower formaldehyde outgasing than ordinary plywood’s. Larch batten forms a service zone between the OSB and the Heraklith used instead of plasterboard. Heraklith is a magnesite bound wood wool board to which two coats of lime render has been applied.
WOODS. Elm and Cherry harvested from sustainable sources on local farms were used for the internal doors, stairs and balustrades. Cladding externally is in vertical Oak Boarding, Larch was used for other structural works; both sourced locally.
WOOL. Welsh wool was sent to Bradford for washing. Loose wool rather than processed slabs proved good for stuffing into all sorts of difficult places. Be aware of the possibility of a moth infestation when using wool insulation. They treated with Borax but still worry when they see anything unidentified in the moth family.
ROOFING An insulated warm roof construction, to overlay the existing exposed rafters and timber boarding, was added. they used expanded polyurethane (Kingspan) insulated board. A high-grade insulation was essential to minimise visual changes to the roof thickness. Further insulation can be added internally but the preservation of the open rafter “roofscape” was a primary consideration. Softwood timber penny gap boarding was laid to support a new external waterproof layer of titanium zinc sheeting. A new vented finial was installed at the apex to allow water vapour to escape.
WALLS It was decided not to insulate the existing masonry walls since this would alter the appearance. Internally the timber panelling would be lost and limited space would be reduced further.
WINDOWS The existing windows were copied using new painted softwood but with double-glazed units and low E glass. They have already had to repair and replace the windows. They need a great deal of maintenance. A small porch would help keep out the winter winds but Planning were not keen.
FLOOR The existing softwood timber floor was taken up and joists laid on new sleeper walls. Second hand oak boarding with 200mm of natural sheep’s wool insulation between and under the joists was used.
HEATING The original building was heated by a very inefficient open fire. This has been replaced by an imported firebrick Finoven, a type of “Kachelhoven” or tile stove, from Holland. These are not common in Britain; it works on a principle of a large thermal mass being heated with a short, fast burn of timber. The stove is then shut down and the heat slowly escapes from the double walled firebrick surround. The stove is built through the thickness of an internal wall between the living room and the shower room. It incorporates a “back boiler” to heat water. An existing alcove in the south wall was utilised to house the solar hot water storage tank, which has a double heat exchanger, one for the solar panel and one for the stove. Solar hot water seems to be enough for normal showering right through the summer.
ELECTRIC LIGHT AND REFRIGERATION. There is an Aerogen self-furling, wind generator running parallel to a photovoltaic solar panel. This turbine, with the PV panel, supplies low voltage electricity for lighting and low power loads required by refrigeration, fans and pumps. The system can be switched to provide 240 volts for a computer or phone charger! Hair dryers and Irons overload the system. There are display boards indicating the amount of power stored and whether it is made by wind or sun.
REED BED DRAINAGE treats the sewerage by separation and a succession of reed beds and ponds, hopefully increasing the species of Dragonfly in the area. An eel has already taken up residence in the pond. Willow has been planted for coppicing as fuel for the stove. The surviving trees are starting to show their qualities after ten years and they hope to coppice next year. The reed bed system is a bit of a “grey” area. they still do not completely understand its mysteries!
PAINTS. Clay based paints have been used. This helps those with allergies.
RAINWATER is collected from the roof is stored underground in a recycled juice container. The loo uses half the amount of water and it has to be the loo with the best view in the entire world. Water is environmentally VERY expensive to purify and they just flush it down the loo. I have seen a wash hand basin (Japanese) that sits over a cistern for a loo and uses the hand washing water to flush. If you know where to get one let us know!
TEN YEARS ON – The Roundhouse is incredibly self sufficient costing about £400 a year in fuel for heating and cooking. The sun and the wind provide all other energy needs. The energy systems have needed to very little servicing although they feel that the wind generator will need something fairly serious in the next year or so. It is the most popular let with guests coming to visit right through the winter. I would feel completely comfortable living there all year round.
More detailed information on the building techniques and systems used is available at the hotel. There is also a list of the specialists if you would like help in the setting up your own eco house.
THE PROJECT is now paid for in full and was achieved with the co-operation of many people and organisations that provided expertise and financial assistance. Architect Julian Bishop led the design team, with specialist help from Bob Williams of Sustainergy on low voltage electrical installation and wind turbine. Cliff Blundell supervised work with limecrete. Jamie Ashe handled the mysterious installation of the Reed bed.
THE BUILDING TEAM, led by Ian Doyle, working against the clock and in the teeth of the storms way beyond the call of duty, are planning some work at the hotel on reducing carbon footprint.
Roundhouse Open Day: Bookings by arrangement only – Fridays are best as that is change over day for residential visits.
Phone … 01437 781221