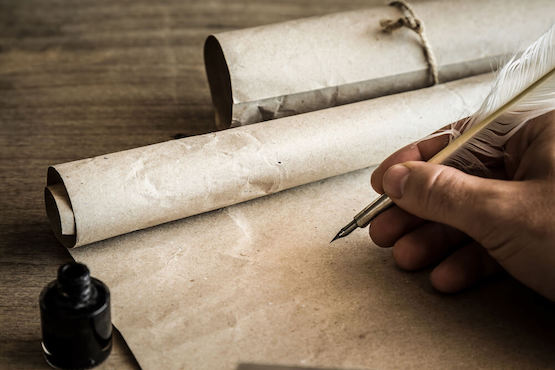
Source: Shutterstock, royalty-free stock photo ID: 697987804
After the initial trauma of the coronavirus lockdown, one can imagine the ease with which civilization might disintegrate in the face of disaster. In a real end of world scenario, we can safely assume that many of the things we take for granted — wireless networks, smartphones, the Internet and other forms of instant communication — will be lost.
For the survivors, then, they will have no choice but to fall back on the more traditional forms of communication — such as the simple pen and paper. But paper is an extremely perishable material. A combination of time, wildfires, humidity and other factors will quickly deplete whatever stocks of paper are left behind.
Civilizations are built on the accumulated knowledge of writers. To avoid a regression, it will be necessary for the survivors of the hypothetical collapse to return the real fruits of the Earth. They will need to learn how to recreate paper from scratch.
Paper from the raw Earth
Chinese civilization was the first to develop paper, perhaps more than a thousand years before it appeared in Europe. But the ancient Chinese did not use the same type of paper that is widely used in society today. In fact, modern smooth and white paper is actually a very recent invention, dating only back to the late nineteenth century.
Before then, paper was mostly made out of tattered and recycled linen fragments. Linen itself is a type of fabric made from the fibres of flax plants. But in principle, paper can be constructed out of any plant that is fibrous in nature. Including from hemp, some types of coarse grass, even nettles.
Modern paper is uniquely light and strong, however, because it is made from fibres that consist mainly of cellulose. This chemical is actually present in all plants. The problem is, it is very difficult and labour intensive to remove cellulose from other plant chemicals. Traditionally, a process known as ‘retting’ would be required. Whereby plant stems are crushed and left to soak in stagnant water for a few weeks. During which the structure is broken down and decomposed by microorganisms. But even after the stalks are softened, the cellulose usually has to be ‘beaten’ out of them by force.
Modern paper — made from tree trunks — is made from a type of cellulose that is intertwined with a very strong chemical called lignin. Fortunately, there is a way to separate the two with minimal effort — by implementing a chemical process known as hydrolysis.
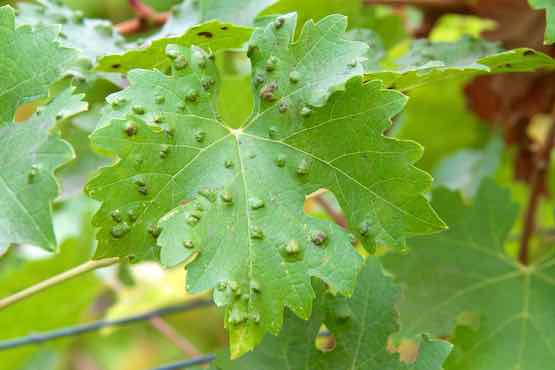
Source: Shutterstock, royalty-free stock photo ID: 504401863
Reinventing modern paper
Hydrolysis is a molecular operation that is used for a variety of reasons across the industrialised world, and making modern paper is no exception. It involves chopping up wood into small pieces and placing it into a vat of boiling alkaline solution for a few hours. The corrosive alkali will soon begin to break down the chemical bonds of the wood.
Alkali will corrode both cellulose and lignin. But importantly it will destroy the lignin more quickly, giving you ample time to separate and clear out the paper-making cellulose fibres beforehand. You will know when the process is complete, because the solution will turn into what looks like a broth of dirty-brown bath water, and the short white cellulose fibres will float on the top of it.
There are many ways to create alkali solutions, and some are more (much) easier than others. The simplest way is to ferment your own urine.
Human beings, like all mammals, flush out excess nitrogen in a water-soluble form called ‘urea’ whenever they urinate. Given enough time and the ideal conditions, microorganisms will readily convert urea into a particularly smelly compound known as ‘ammonia’. If you have ever visited a poorly cleaned public toilet, the chances are you have smelled ammonia before.
Ammonia-induced hydrolysis may not be the most efficient method available, but it is incredibly low tech and easy to do. At the very least, it is a starting point for moving on to more advanced methods.
When it looks ready, collect the white cellulose fibres and rinse them clean of any traces of the muddy broth (this is the disintegrated lignin). You should eventually have a thick ‘porridge’ of sloppy cellulose. Finally, you will need a fine wire mesh or framed cloth screen. Pour the cellulose over the mesh and, once the excess water starts to evaporate, the fibres will eventually mesh together into a mat. Keep squeezing it to get it as smooth as you want and let it dry and there you have it. Smooth sheets of naturally-made paper.
Manufacturing ink from the raw Earth
Paper won’t be much good without ink. Once all the ink pens have vanished from the Earth, the survivors will need to reinvent it. Technically, anything that stains can be classed as an ‘ink’. You could easily mash up some fruit, preserve it in salt, and use that as an ink.
What’s really important for an effective ink-type, however, is that it stays around. Good ink is therefore hard to erase, and ideally permanent once committed to paper. This is to prevent information from being lost.
In the middle-ages, the Europeans discovered iron gall ink, which is still the ink of choice in many courtrooms today, where it is known as “registrar’s ink”. It is incredibly resistant to sunlight and cannot easily be scrubbed off.
‘Galls’ look like tiny warts on plants and appear when parasitic wasps irritate the plant’s surface. Importantly, they are heavy with tannic and gallic acids that, when mixed with iron, can be used to make an ink that eventually dries into a deep, permanent black.
Manufacturing a rudimentary pen
With ink and paper, you will need a pen. Fortunately, this is the easiest of all to recreate. Anyone who has seen a caricature of medieval society in popular media will know that you can make a pen out of a feather.
The best quills are made from duck or swan feathers. All you will need to do is remove the material from the shaft of the feather, and then sharpen the base into the classic shape of a writing nib. This nib should have a slight slit backwards in order to allow for a tiny amount of ink to sit on it, reducing the amount of times it will need replenishing from an inkwell.
Reinventing the printing press
Arguably one of the most important inventions of all time is the moveable-type printing press, which originated in Germany in the fifteenth-century. The first ever printing press was just a row of cuboidal blocks in a rectangular frame with a different letter emblazoned on each. The cubes would be inked and then pressed on to the paper.
Even a rudimentary printing press, like the one described above, is hundreds of times faster and more efficient than scribing. But it involves the painstaking process of organising blocks in the order of a written page of text, pressing the ink on to paper, and then reorganising the blocks and repeating for the next page.
There are two things you will need for an effective printing press: the technology to efficiently do the ‘pressing’ of ink on to paper, and a way to make identical letter typecast moulds.
For the second point, the easiest way to make typecasts in this way is to make them with straight smooth sides, but also with right-angled edges. This is so they can slot perfectly alongside other typecasts to form rows of blocks.
The shape of the letters can be made on the end face of the block by placing a swappable matrix at the mould’s base. You can make matrixes like this out of malleable metals like copper. The indents of the individual letters or numbers can then be hammered into them with a single steel punch.
With this method, you will only have to make the one engraving of each letter, number, and symbol on to different punches. Which should then make it near effortless to churn out pieces of identical type.
The last major obstacle is that of a forceful mechanical device to act as the press. This technology is still widely used today, which is why they still call it the printing ‘press’. If the survivors are unable to salvage any of this technology from the ruins of civilisation, then a simple lever or pulley system should work.
Ink for the printing press
Unfortunately, a new type of ink will need to be reinvented for use on the printing press. You will need what’s known as a ‘viscous ink’. One that will transfer clearly to the paper when pressed, and one that won’t blur or smear afterwards.
You can make this new ink out of soot. The tiny particles of soot act as a dark pigment when mixed with water and a linseed or walnut oil (which will act as a thickener). If you have turpentine to use as a thickener, then even better. You can vary the stickiness and thickness by adjusting how much thickener you add to the soot and water. But either way you should have a mixture that will dry and stick well when applied to the press.
Reinventing advanced civilisation
Isaac Newton once famously said that “If I have seen further, it is by standing on the shoulders of giants”. By drawing on the intellectual musings and writings of countless generations before him, and the knowledge preserved in libraries of books, he had a great advantage that allowed him to put forward his theory of gravity and Newtonian physics.
Civilisations that preserve the written language can accumulate knowledge and advance in ways that oral societies cannot. Reinvent writing, ink, and the printing press, and you will reinvent one of the most important technological mechanisms in all of human history.
—
This Author
Neil Wright is from McGowan Transcriptions.