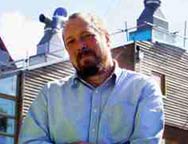
Dunster: trying to get it right
House building eco-kits combine sustainability with lower unit costs, says leading eco-architect Bill Dunster.
AFTER gaining valuable/salutory experience from Beddington Zero Energy Development, the UK’s first attempt at a carbon-neutral eco-community, the team at Dunster’s architect firm, ZEDfactory, were sure they knew how to reduce construction costs and refine designs for other carbon-neutral schemes.
Their first project may have been a glorious failure, but this time, they might be about to get it right.
They reason that nobody wants to pay a premium for extra design and engineering time in eco-projects. And why should they? Bill Dunster says: ”We were ambushed by the application of traditional design codes on Government-controlled sites and reluctance to discuss improvements on the BRE eco-homes standards. It seemed raising standards was seen as a threat to delivering maximum numbers of affordable new homes.” Looking for alternatives to current practices, the team put forward to the Government its own lowcarbon roadmap.
They calculated that by applying these across just 3 per cent of the Sustainable Communities programme they could reduce any premium above current building regulations to zero.
Dunster says: ”This led to our new fast build, dry construction, zero-carbon house kit, called RuralZED. It had to accommodate perimeter block layouts required by traditional design codes, work to a lower density of 30 to 50 homes per hectare, and have sufficient integrated renewable energy systems, which combine wind and solar power, to approach carbon neutrality.” Many say maximising passive performance of the building fabric through solar gain, thermal and photovoltaic panels, wind turbines and super-insulation is the best way to make renewable energy a viable national strategy.
So, with funding from the Housing Corporation on behalf of the Cornwall Sustainable Building Trust, ZEDfactory began developing a prefabricated RuralZED kit, complete with assembly manual and training course.
Mr Dunster says: ”After the hot summer of 2003 we knew overheating from climate change meant we had to find a way of creating a flatpack kit to meet the Government’s definition of a modern method of construction.
”The solution was to cast eco-concrete panels into prefabricated planks that could be bolted onto pre-cut frames designed to carry the extra weight. The concrete used was often less than that required by a conventional timber frame on mass concrete strip foundations.” The first RuralZED frame kit was erected in 2006 in the Cornish regeneration zone of Camborne and attracted favourable interest from the local community. Since then ZEDfactory has moved into a production phase. Build costs are currently